-
Valve installation precautions
.jpg)
After the correct selection of the valve, it must be properly installed, maintained, and operated so that its performance can be fully utilized.
The quality of the valve installation directly affects the use, so care must be taken.
1. Direction and position
Many valves have directionality, such as cut-off valve, throttle valve, pressure reducing valve, check valve, etc. If the device is reversed, it will affect the use effect and life (such as throttling valve), or it will not work (such as Relief valve) and even dangerous (such as check valve). General valves, there are directional signs on the valve body; if not, should be correctly identified according to the working principle of the valve.
The valve chamber of the shutoff valve is asymmetrical in right and left direction. The fluid should be allowed to pass through the valve port from bottom to top, so that the fluid resistance is small (determined by the shape), and the effort is saved (due to medium pressure upwards). After closing, the medium does not press the filler, facilitating maintenance. . This is why the shut-off valve cannot be reconciled. Other valves also have their own characteristics.
The position where the valve is installed must be easy to operate; even if the installation is temporarily difficult, it is also necessary for the operator's long-term work. The best valve hand wheel and chest (usually 1.2 meters away from the operating floor), so that the opening and closing of the valve is more energy efficient. The landing valve handwheel should face upwards, do not tilt, so as not to operate awkwardly. To rely on the valve of the machine by the wall machine, but also to leave the operator to stand. Avoid going to heaven, especially acid and alkali, toxic media, etc. Otherwise, it is not safe.
The gate valve should not be flipped (ie, the handwheel is down), otherwise it will cause the medium to stay in the valve cover space for a long time, and it is easy to corrode the valve stem, and it is contraindicated for certain process requirements. It is inconvenient to replace the packing at the same time
Do not install the underground gate valve, otherwise it will corrode the exposed valve stem due to moisture.
Lifting check valve, to ensure that the valve flap vertical when installed, in order to lift and flexible.
Swing check valve, to ensure the level of its pin axis during installation, so that the spin is flexible.
The pressure relief valve should be installed upright on a horizontal pipeline. Do not tilt it in all directions.
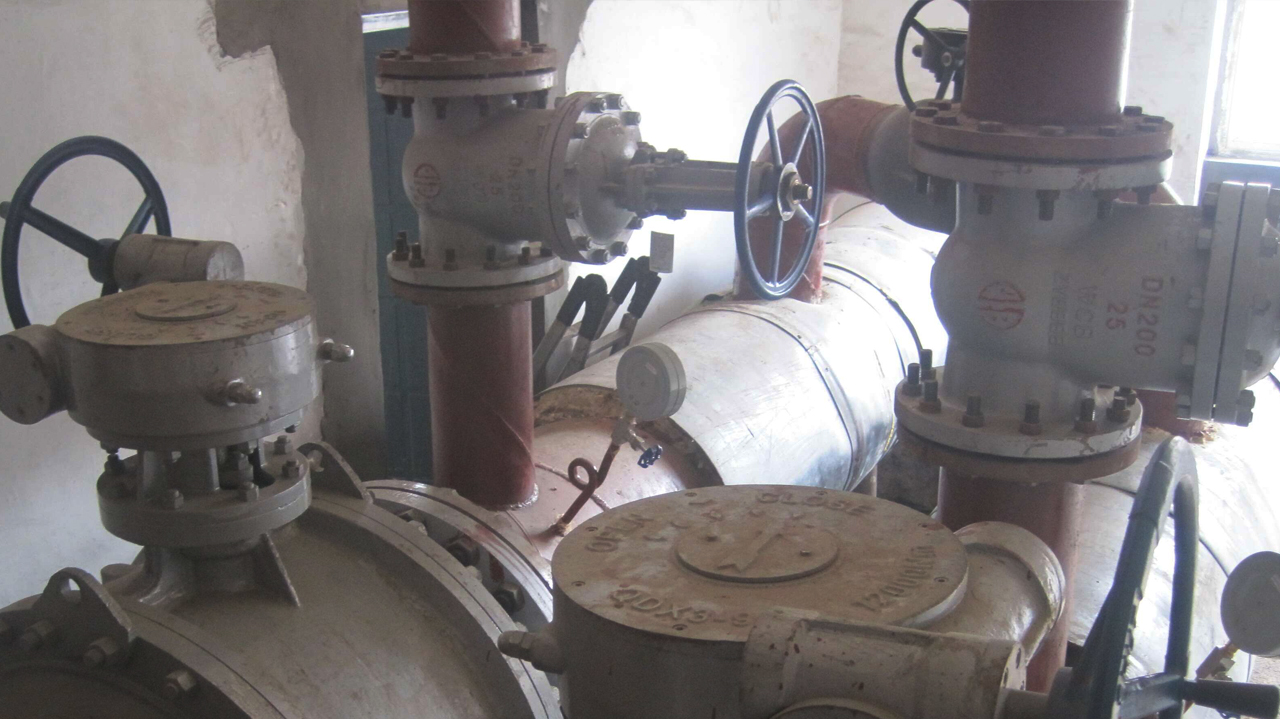
2. Construction work
Care must be taken in the installation and construction. Do not strike valves made of brittle materials.
Prior to installation, the valve should be checked to verify the specification and type, and identify any damage, especially for the valve stem. Also, rotate it a few times to see if it is skewed because it is the most likely to hit the stem. Also remove debris from the valve.
When the valve is lifted, the rope should not be tied to the handwheel or valve stem to avoid damage to these components and should be tied to the flange.
For the pipe to which the valve is connected, it must be cleaned. Compressed air can be used to blow away iron oxides, mud sand, welding slag, and other debris. Such debris not only scratches the sealing surface of the valve, but also causes large particles (such as welding slag) to block the small valve and cause it to fail.
When installing the screw valve, seal packing (line hemp plus lead oil or PTFE raw material tape) should be wrapped on the pipe thread, do not get into the valve, so as not to accumulate in the valve and affect the medium circulation.
When installing a flanged valve, be careful to tighten the bolt symmetrically and evenly. The valve flange and the pipe flange must be parallel and the clearance is reasonable, so as to avoid excessive pressure on the valve and even cracking. For brittle materials and low strength valves, pay special attention.
Valves that must be welded to the pipe should be spot welded first, then the closure must be fully opened and then welded.
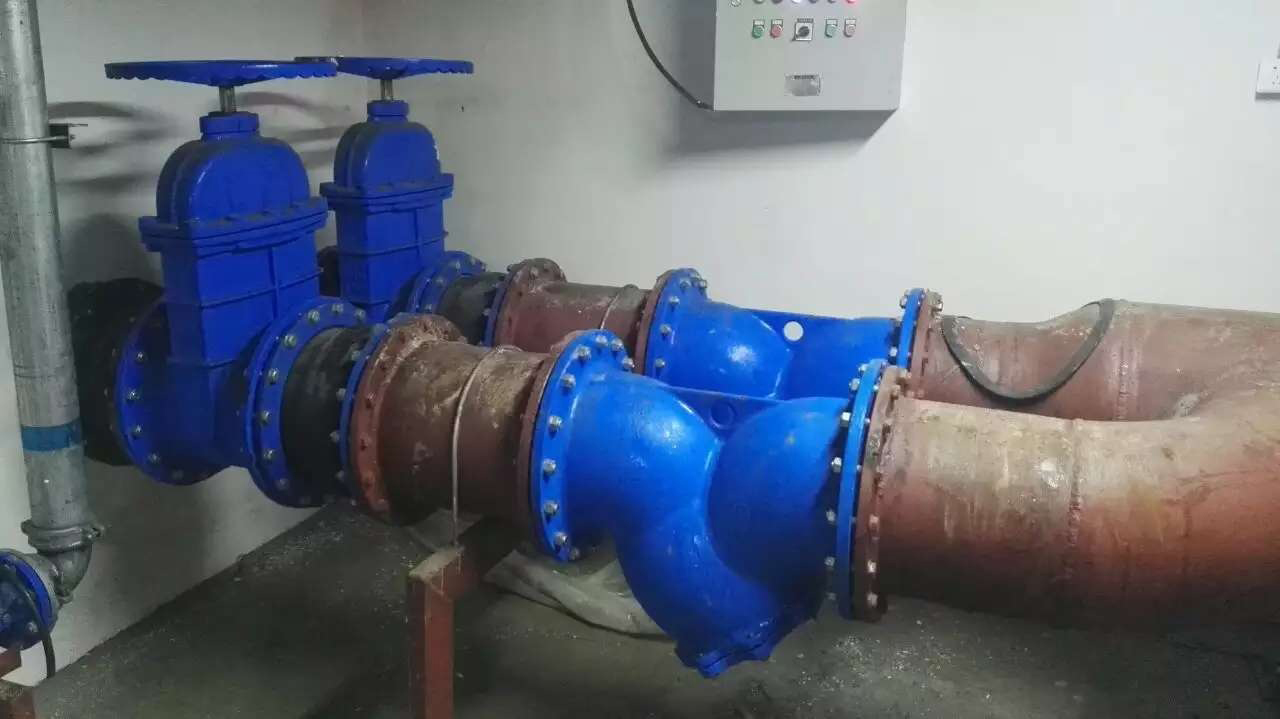
3. Protection facilities
Some valves also require external protection, which is insulation and cooling. Heat traces are sometimes added to the insulation layer. What kind of valve should be kept warm or cold, according to production requirements. In principle, if the medium in the valve lowers the temperature too much, it will affect the production efficiency or freeze the valve. Therefore, insulation or even heat is needed. When the valve is bare, and it is unfavorable for the production or causes frost and other undesirable phenomena, it needs to be kept cold. Insulation materials include asbestos, slag wool, glass wool, perlite, diatomaceous earth, vermiculite, etc.; cold insulation materials include cork, perlite, foam, and plastics.
Long-term unused water and steam valves must drain water.
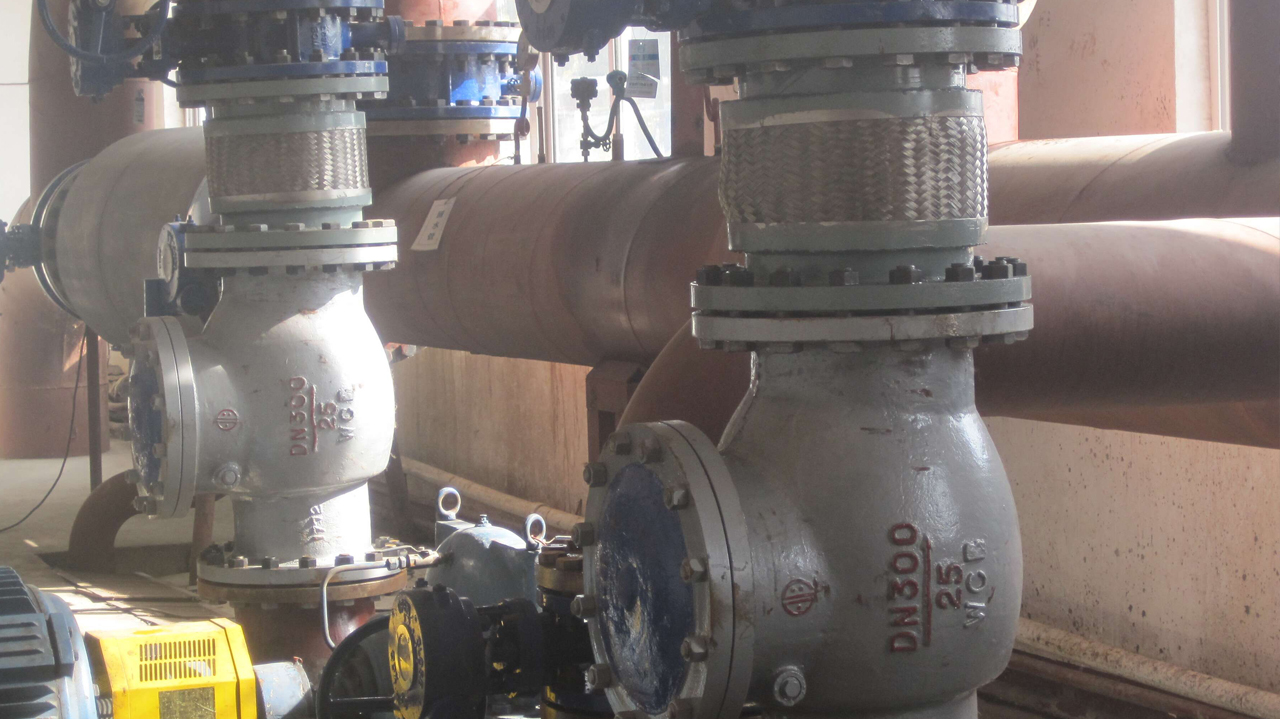
4. Bypass and Meter
Some valves, in addition to the necessary protection facilities, also have bypasses and meters. Bypass is installed to facilitate trap servicing. Other valves are also installed bypass. Whether or not to install a bypass depends on the condition of the valve, its importance, and its production requirements.
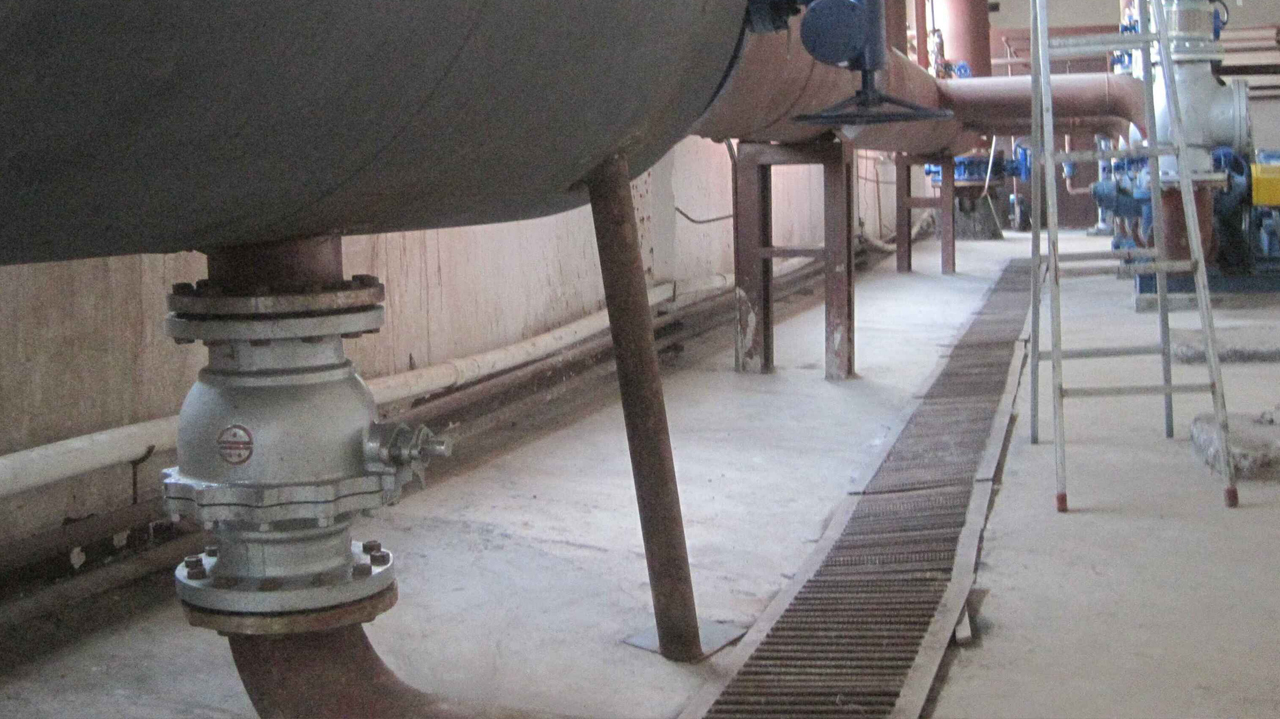
5. Filler replacement
Inventory valve, some fillers are not good, and some do not match the use of media, which requires the replacement of filler.
Valve manufacturers can not consider the use of different types of units of thousands of medium, stuffing box is always filled with ordinary packing, but when used, must make the filler and media compatible.
When replacing the packing, press it in a circle. 45 stitches are appropriate for each seam, and the stitches are staggered by 180 degrees. Filler height to consider the continued compression of the cover of the room, and now also to make the bottom of the pressure gland to press the appropriate depth of the chamber, this depth can generally be 10-20% of the total depth of the filling chamber.
For demanding valves, the seam angle is 30 degrees. The seam is staggered by 120 degrees.
In addition to the above-mentioned fillers, according to the specific circumstances, but also according to specific circumstances, the use of rubber O-rings (natural rubber resistant to less than 60 degrees Celsius, nitrile rubber resistant to oil below 80 degrees Celsius, fluorine rubber resistance to 150 degrees Celsius below a variety of corrosive media) three Stacked PTFE ring (strong corrosion resistance below 200 degrees Celsius) Nylon bowl ring (resistant to ammonia, alkali below 120 degrees Celsius) and other forming fillers. Outside the ordinary asbestos packing, a layer of PTFE tape is used to improve the sealing effect and reduce the electrochemical corrosion of the valve stem.
When pressing the packing, the valve stem must be turned at the same time to keep it evenly around, and to prevent it from dying too much. Tighten the cover tightly and do not tilt it.