-
How does the valve are corroded
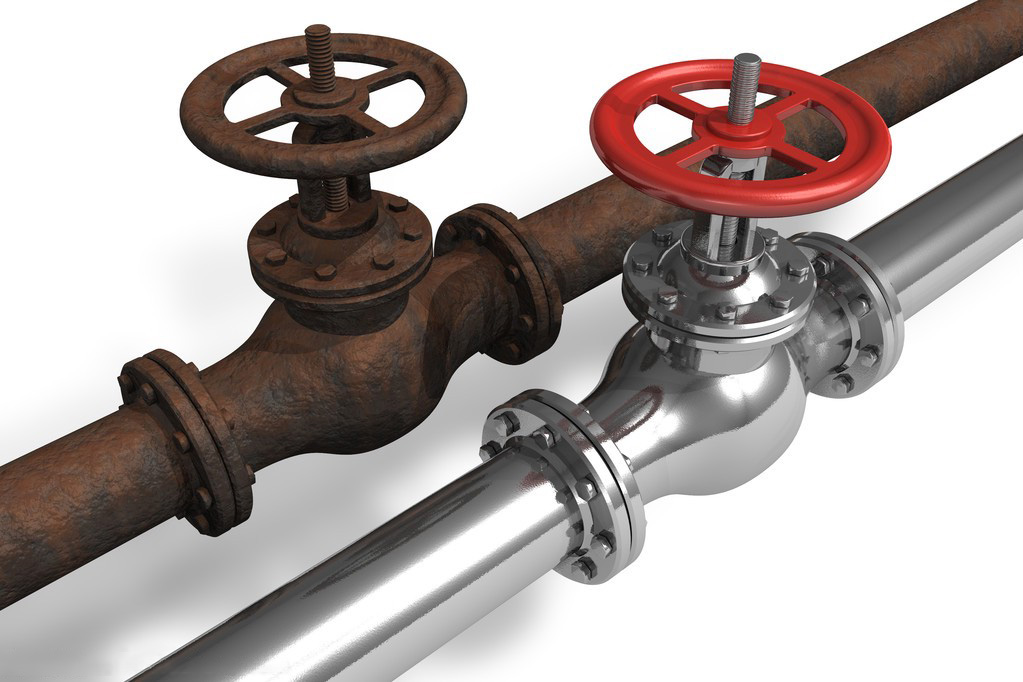
When two different metals are in contact and exposed to corrosive liquids and electrolytes, forming the original battery, the current makes the anode corrosion increase the current. Corrosion is usually near local contact points. Reducing corrosion can be achieved through electroplating alien metals.
High temperature corrosion
In order to predict the effects of high temperature oxidation, we need to examine these data: 1) metal composition, 2) atmosphere composition, 3) temperature, and 4) exposure time. However, it is well known that most light metals (those who are lighter than their oxides) form a non -protective oxide layer, which will fall off as time goes thicker and thicker. There are also other forms of high temperature corrosion including vulcanization, carburizing, and so on.
Gap corrosion
This all happens in crevices, which impede the diffusion of oxygen, creating regions of high and low oxygen, resulting in differences in solution concentration. In particular, narrow gaps may occur at the defects of connecting parts or welded joints, The width of the seam (generally 0.025~0.1mm) is enough for the electrolyte solution to enter, so that the metal in the seam and the metal outside the seam form a short-circuit galvanic battery, and strong local corrosion occurs in the seam.
Pitting corrosion
When the protective film is destroyed or the corrosion product layer is decomposed, localized corrosion or pitting corrosion occurs. The membrane ruptures to form the anode and the unbroken membrane or corrosion product acts as the cathode, effectively creating a closed circuit. Some stainless steels are prone to pitting corrosion in the presence of chloride ions. When corrosion occurs, these are not uniform on the metal surface or roughness.
Crystal corrosion
Intergranular corrosion occurs for a variety of reasons. The result is almost the same breakdown of mechanical properties along the metal grain boundaries. Intergranular corrosion of austenitic stainless steels at temperatures of 800–1500°F is susceptible to many corrosive agents (427–816°C) without proper heat treatment or contact sensitization. This condition can be eliminated by pre-annealing and quenching to 2000°F (1093°C) with low carbon stainless steel (c-0.03 max) or stabilized niobium or titanium.
Frictional corrosion
The physical force of fracture from wear, dissolving metals through protective corrosion. The effect depends mainly on force and speed. Excessive vibration or metal bending can have similar results. Cavitation is a common form of corrosion in pumps, and stress corrosion cracking, high tensile stress and corrosive atmospheres can cause metal corrosion. Under the action of static load, the tensile stress of the metal surface exceeds the yield point of the metal, and the corrosion is concentrated in the area where the stress is applied, and the result is shown as a localized corrosion. Alternate corrosion of metals and build up of high stress concentrations in parts, this corrosion can be avoided by early stress relief annealing, or the selection of appropriate alloy materials and design schemes. Corrosion fatigue We often associate static stress with corrosion.
Stress can lead to corrosion cracking, and cyclic loading can lead to fatigue corrosion. Fatigue corrosion occurs when the fatigue limit is exceeded under non-corrosive conditions. Surprisingly, the coexistence of these two types of corrosion is even more harmful. That's why we use the best corrosion protection measures under alternating stress.